Manufacturers have been responding to supply chain disruptions and other industry challenges by replacing their outdated technology. If you’re thinking about following suit, then this list of the top 10 manufacturing ERP systems and examples of solutions is for you.
The 2024 Top 10 Manufacturing ERP Systems Report is designed to help manufacturers across verticals understand what kind of functionality is available in the market today.
(Note: The ERP providers and vendors featured in this report were chosen by our ERP experts based on what vendors they are most frequently asking for RFPs and demos for manufacturing clients. The order of listing is alphabetical and not based on ranking.)
he Top 10 ERP Systems for the Manufacturing Industry
1. Acumatica Cloud ERP
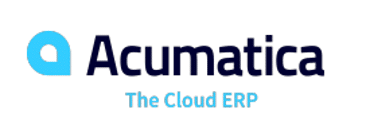
Acumatica Manufacturing Edition is a suite of connected business applications that provides manufacturing depth for production, estimating, engineering, material planning, scheduling, product configuration, and manufacturing data collection.
2. Cetec ERP

Cetec ERP is a web-based, fully integrated business suite for small and mid-sized manufacturers and distributors. The platform includes functionality for supply chain & inventory control, CRM & purchasing, production tracking & scheduling, quality control, and accounting & financials.
3. Epicor Kinetic
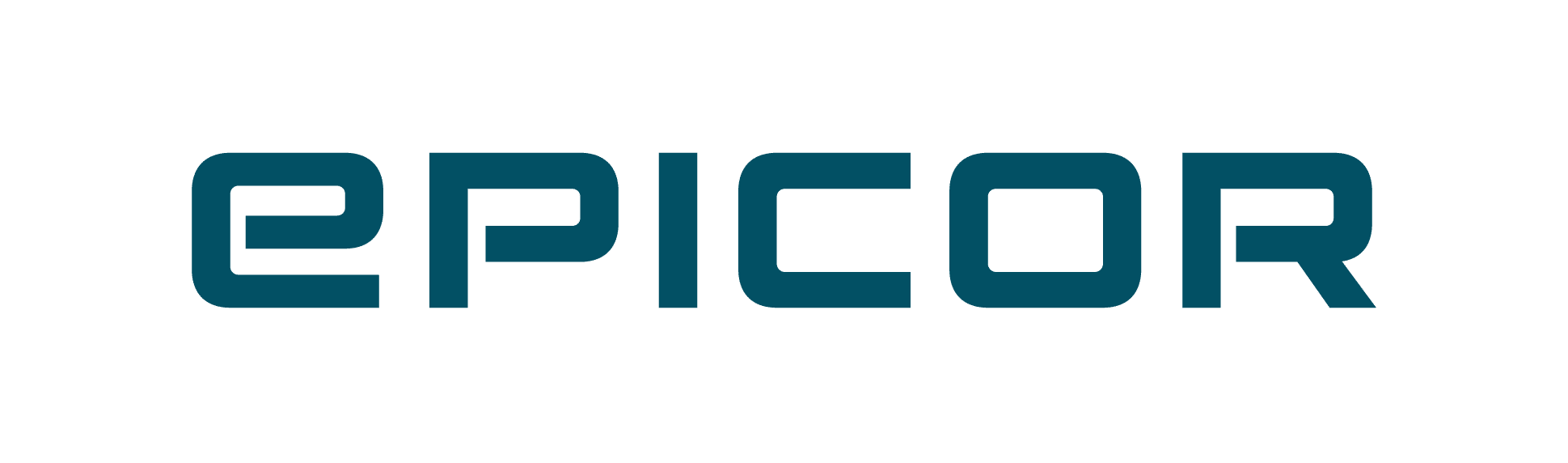
Epicor Kinetic is a manufacturing tool with a full range of supply chain management capabilities. This cloud ERP system includes industry-specific solutions, like APS, MES, and CPQ, which can be extended as you grow.
4. IFS Cloud
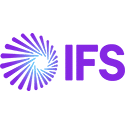
IFS Cloud is an industry-focused solution tailored for large and mid-sized organizations. The solution combines Enterprise Resource Planning, Service Management, and Enterprise Asset Management capabilities.
5. Infor Manufacturing Cloud ERP
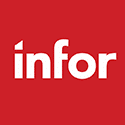
Infor’s industry-specific CloudSuites include ERP and SaaS cloud applications designed for manufacturing industries at the enterprise level and small to medium-sized businesses. Infor’s CloudSuites are cloud-native and available as a service within a secure cloud environment powered by Amazon Web Services.
6. Microsoft Dynamics 365 Finance/Supply Chain & Business Central
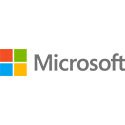
Both of these Microsoft solutions include the power of the Microsoft platform, which provides integrated reporting and visualization. Business Central is a lower-cost solution that provides a faster time to value.
7. NetSuite ERP
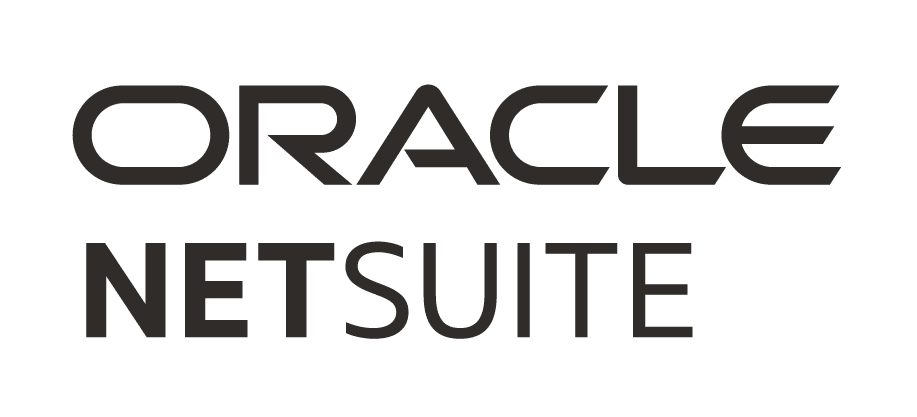
NetSuite ERP is a full suite of cloud-based ERP applications that help growing manufacturers plan, control, coordinate, and manage every aspect of their operations in one place.
8. Oracle Fusion Cloud Supply Chain & Manufacturing

Oracle Fusion Cloud is a full suite of supply chain and manufacturing applications with functionality for supply chain management, finance, human resources, and customer experience.
9. Priority ERP
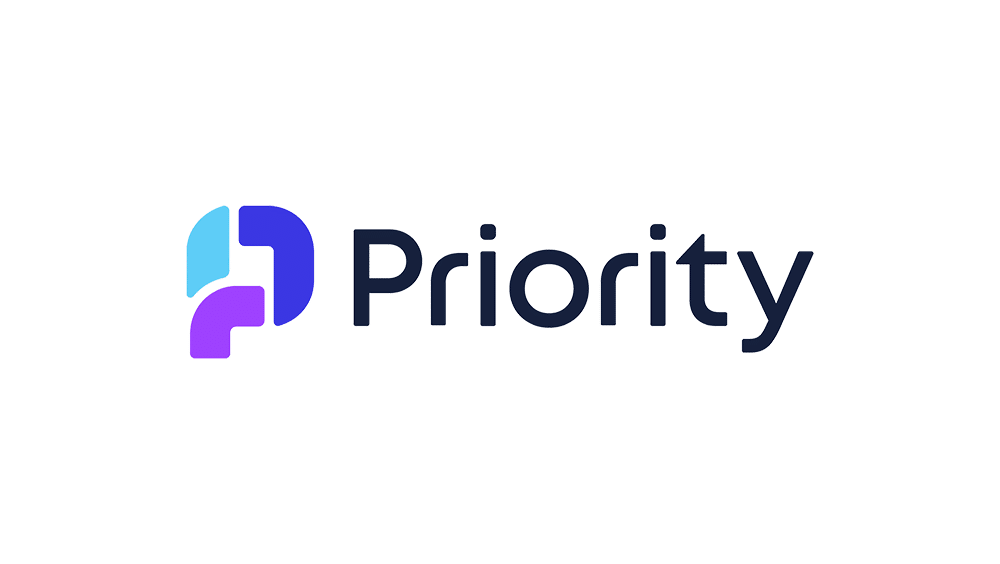
Priority ERP is a scalable, open SaaS cloud ERP platform for organizations of all sizes. It is designed for industries such as manufacturing, wholesale and distribution, electronics, healthcare, medical devices, pharmaceutical, nonprofit, construction, professional services, financial services, retail, and more.
10. SAP S/4HANA
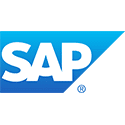
SAP S/4HANA includes ready-to-run cloud ERP software for manufacturing companies. It supports all forms of both discrete and process manufacturing in a single solution, including make to stock/repetitive, make to order, configure, and engineer to order.
You can find more information on the functionality of each system by downloading our 2024 Top 10 Manufacturing ERP Systems Report:
2024 Top 10 Manufacturing ERP Systems Report
Are you a mid- to large-sized manufacturing firm? This report is for you. Download it now to learn what kind of advanced functionality is available in the market today.
In the meantime, we’d like to share a few best practices for selecting the best ERP system for manufacturing companies. Here are some expert insights that will prepare you for a successful ERP provider selection and implementation in the manufacturing industry.
The First Step in Manufacturing ERP Selection: A Business Case
Before beginning ERP selection, you need executive buy-in and clearly defined business goals. A business case can help in both regards.
When developing a business case, consider what has sparked your search for new manufacturing ERP software. Was it the need for advanced analytics for production scheduling? Was it the recognition that your order management or customer experience could use improvement?
Regardless of the reasons, it’s important to outline them and quantify your expected business benefits. A strong business case that outlines tangible benefits and ties these back to bottom line revenue works wonders in convincing executives to invest in ERP.
The benefits of modern manufacturing ERP software are numerous. For example, as a manufacturer, you likely have hundreds, if not thousands, of SKUs, making it challenging to track inventory.
If this sounds familiar, you can make the case for implementing a modern manufacturing ERP system by demonstrating how the system could integrate various departments and simplify inventory management and inventory control. This is possible because the CRM functionality within most modern ERP solutions fully integrates with your shop floor and enables more accurate reporting.
Another example relevant to today’s manufacturers? Say you want to meet your customers’ expectations regarding a flexible purchasing process. In your business case, you could highlight ERP’s ability to facilitate the user-friendly purchasing that B2B consumers have come to expect.
Once you understand your business goals, you can evaluate the top ERP systems for manufacturing based on their ability to support your goals. This will help you find not only the best ERP for manufacturing but the best ERP for your unique needs.
3 Overlooked ERP Implementation Success Factors
Our manufacturing clients have historically been in industries such as industrial manufacturing, chemicals, food and beverage, and consumer products, among others. Through this experience, we’ve found that regardless of a company’s sub-vertical, there are certain success factors that are frequently de-prioritized.
Here are some ERP implementation best practices that manufacturers often overlook:
1. Building an Internal Project Team
From project managers to executive sponsors, the skillsets and background of the people working on your project matter. Your final team should include stakeholders from across your organization who can rely on backfilling to make the project a priority.
2. Improving Business Processes
Conducting business process improvement before ERP selection can help you understand where pain points exist and what processes your employees would like to overhaul.
For example, if employees are experiencing pain points around order fulfillment, you may need to integrate your demand forecasting and advanced planning processes with your inventory and sales processes.
Regardless of your specific pain points, improving your processes can help you define software requirements and effectively communicate with ERP vendors.
3. Focusing on Change Management
Enterprise software implementations often go awry because organizations fail to anticipate how their workforce will react to the change.
By developing an organizational change management plan, you can begin to view the change from the employee’s perspective. Key change management deliverables include but aren’t limited to a sponsorship roadmap, a resistance management plan, a communication plan, and an ERP training strategy.
The Best ERP software for the Manufacturing Industry Doesn’t Always Equal Success
ERP success doesn’t begin with a list of the top manufacturing ERP systems, but it’s an important part of the journey.
To learn more about manufacturing ERP functionality, download our 2024 Top 10 Manufacturing ERP Systems Report, and to learn how to find the best ERP provider for your company in particular, request a free consultation below. You’ll have the opportunity to speak with our ERP consultants and discuss your unique business needs.