It’s no secret that modern enterprise resource planning (ERP) software is a great way to consolidate your business functions. It also can increase operational efficiency, produce cost savings and centralize data throughout the enterprise.
Clearly, ERP systems have a wide range of benefits, but how can you convince executives of the ROI? What arguments will you need to make, and what goals will you need to quantify?
Here, we’re going to help you develop a solid ERP business case that’s sure to convince your boss to give you an adequate ERP budget.
Contents
1. 4 Reasons You Need an ERP Business Case
2. How to Build a Business Case
3. How to Convince Executives
4. 8 Reasons to Replace or Upgrade Your ERP System
5. Why Businesses Should Replace Their ERP Software at Least Every Ten Years (internal factors as well as external factors, such as the economy)
6. Conclusion
4 Reasons You Need an ERP Business Case
1. You Won’t Achieve What You Don’t Measure
A business case ensures your company realizes measurable business benefits from its ERP software. In other words, it ensures the project achieves business goals, not just IT goals.
The 2024 Top 10 ERP Systems Report
What vendors are considering for your ERP implementation? This list is a helpful starting point.
Most companies don’t realize the benefits of ERP right away. It can take months or years to realize the full potential of new ERP software. However, you won’t ever achieve many of those benefits if you don’t understand where you’re falling short.
Once you identify where you’re falling short, you can identify the root causes of suboptimal benefits and take corrective action. Sometimes, these are very simple fixes, such as refresher end-user training, tweaks to business processes or modifications to the way the software is implemented.
Other times, you may need to rework your whole project plan.
2. You Need to Validate Your Need for ERP
Often, we hear executives say, “The business case doesn’t matter because we need new ERP software either way.” This may be true sometimes, but often, there are other options that could solve your problem, such as upgrading the current software or facilitating business process reengineering.
While a business case could validate your original line of thinking, it could also reveal better courses of action.
3. ERP Failure is Imminent When a Project Lacks Direction
Many companies don’t realize that a business case helps the implementation succeed just as much as it optimizes post-implementation business benefits. So, how does a business case help ensure success? It does this by providing ERP project team members with clear direction and priorities.
For example, ERP failures are often caused by too much ERP customization. However, with a solid business case, the project team will be better equipped to decide where customization makes sense.
A business case also includes performance measures and targets that you can use to hold team members accountable throughout implementation.
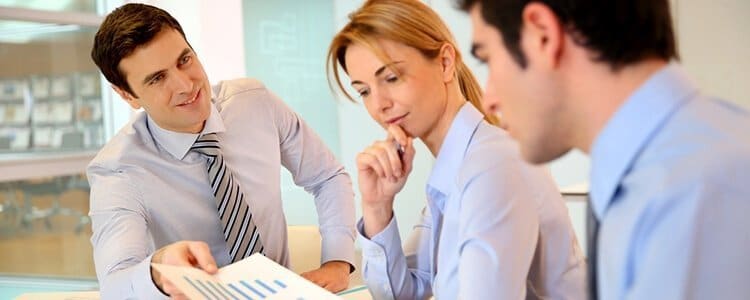
4. You Need to Acknowledge Challenges and Risks
A business case allows you to take an honest look at obstacles that must be overcome, whether it’s a lack of resources, lack of expertise or lack of employee and executive buy-in.
We have seen many high-profile cases where ERP implementations failed because those responsible for implementing the system were not forthcoming about potential risks.
How to Build a Business Case
1. Identify Issues with Your Current Systems
Before you can talk about the reasons you want to implement a new business system, you’re going to need to prove that there are issues with the way your business is currently operating. After all, executives won’t want to pay for a system change unless they see that the old system is causing issues.
We recommend beginning your ERP business case by discussing the issues your business is currently experiencing. For example, you may be experiencing data inconsistencies that lead to late shipments.
If this is the case, explain how ERP software integrates multiple functions into one system – purchasing, manufacturing, distribution and sales all have access to the same, real-time data.
2. Quantify Business Benefits and the Costs of Inefficiency
Once you’ve shown some high-level benefits, it’s time to provide more detail by quantifying specific ERP business benefits. This tells executives that you’ve done your research and can speak their language.
When we help clients develop business cases, we encourage them to ask employees about their pain points. These pain points often can be quantified in terms of their cost to the business.
For example, many clients have employees performing manual processes that could be streamlined through automation. The cost of this inefficiency is very tangible, even though it may not seem as concrete as the known line items on your project budget.
Your employees, customers and executives are all feeling these costs, so it’s your job to quantify them. These costs will become even more real once you define how much time is being wasted on current activities and how much time you could save by automating some of those processes.
If you’re not sure where to start, here are some questions to ask yourself:
- Are you using multiple software solutions for different business processes and none of them talk to each other?
- How difficult is it to get the information you need to run your business?
- Is your IT department swamped trying to maintain several disparate software systems?
- Do your processes and systems enhance the customer experience and lead to a desirable cycle of sales, operations, delivery and satisfaction?
Depending on your answers to those questions, here are some potential business benefits you may want to outline in your business case:
- Reduced inventory levels through improved planning and forecasting
- Reduced materials costs through improved accounts payable practices
- Reduced labor costs through improved allocation and efficiency
- Minimized interruption and shortages through improved production and scheduling
- Improved customer service through on-time shipments and shorter order-to-shipment cycles
- Improved accounting practices through shorter sales cycles
- Improved legal and regulatory compliance
Streamlined and integrated business processes through standardization across departments
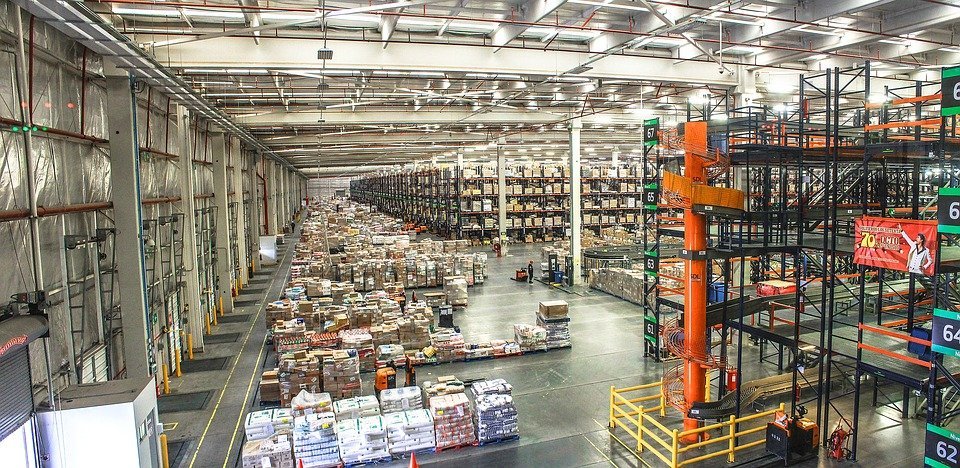
3. Define Your Business Goals
Once you understand the pain points of your current systems, it’s time to ask executives what overall changes they’d like to see in the business. You can use this insight to determine what ERP benefits to highlight.
Do executives want increased visibility across the company? Then, talk about the advanced reporting capabilities of modern ERP software.
Do executives want to the transform the customer experience? Talk about how CRM functionality can personalize touchpoints along the customer journey.
If you’re like most clients we work with, you may not have any doubt that a new ERP system is right for you simply because your legacy system is so outdated. However, this isn’t a good enough reason to implement ERP. You must define what exactly you want to get out of a new system:
Improving Customer Service
Every business case should consider the customer service benefits of new ERP software. Does your company want to enable customers to order online 30% faster once an ERP solution is implemented?
Improving Business Processes
If your operational pain points are related to broken or inefficient business processes, then outline these processes in your business case. Potential process improvements should be specific and measurable.
Improving Employee Morale
An ERP system can improve employee morale by making employees’ jobs easier. Employee morale is measurable since it can be gauged by distributing surveys, conducting focus groups and tracking turnover rates.
Increasing Revenue
Are your employees spending too much time on mundane, repetitive processes? Present that information in terms of lost productivity and labor costs. Are you continually missing deadlines? Calculate the penalties you’ve had to pay as a result. Sound financial reasoning sets your recommendation off on the right foot.
4. Estimate Project Duration and Costs
ERP projects can cost millions of dollars and can last years. There’s no reason to hide these estimates from executives – they’ll find out eventually.
We recommend providing realistic cost benchmarks based on your project scope, company size and industry. This allows you to demonstrate how the benefits of ERP outweigh the costs. In other words, what’s the ROI?
Similarly, realistic timeframes help executives understand when they can realistically expect to recoup costs and see benefits realization.
When developing benchmarks, we don’t recommend relying on time and cost estimates from the ERP vendor alone. These estimates often do not include success factors, such as comprehensive organizational change management and business process management.
5. Consider Alternatives to ERP
We often find that employees’ pain points are more related to process issues than technology issues. While this may not be the case for your company, you’ll still want to show that you’ve considered this possibility because executives like to see that you’ve investigated less expensive options.
If you do find that process issues may be more of a problem than technology issues, it can be helpful to hire an ERP consulting firm that doesn’t force you toward a new ERP system when process improvement or a system upgrade may be a better option in the short-term.
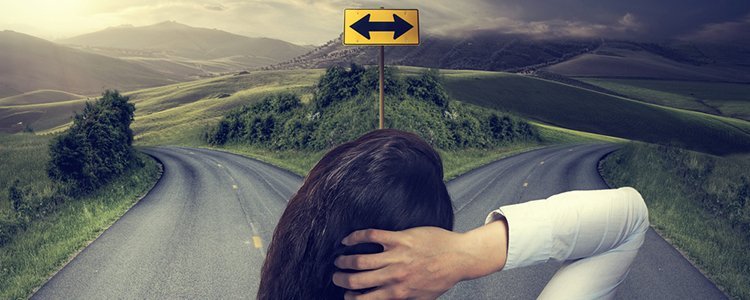
6. Acknowledge Risks and Prepare for Tough Questions
Executives are likely going to anticipate project risks and ask you if the potential benefits are worth the possibility of failure. The best thing you can do here is to acknowledge the risks and show how you plan to mitigate them.
One way to mitigate risk is through organizational change management.
If your company’s change management initiatives have failed in the past, you can discuss the lessons learned from these failures and how you plan to apply these lessons to the next initiative.
Aside from the risk of change resistance, executives may be worried that they cannot afford to take people out of production to implement the ERP system. In cases like this, it’s important to have a counter proposal and hard financial data on why the company cannot afford to continue business as usual.
7. Convey a Sense of Urgency
Executives may anticipate organizational resistance, and they may consider this a sign that it’s not the right time to implement new technology. However, if your business case conveys a sense of urgency, then executives will be less likely to consider change resistance a legitimate excuse for postponing the decision.
While change resistance might mean the company isn’t fully ready for an ERP project, it doesn’t mean there’s no expedient way to prepare employees. We recommend starting with a organizational readiness assessment to determine sources of resistance and identify how those barriers can be removed.
8. Use the Business Case to Develop KPIs
Key performance indicators (KPIs) are a set of concrete measurements that a company uses to track its performance over a period of time. While building a business case, it’s important to create KPIs for each of your expected business benefits.
These KPIs will be helpful down the road when you’re implementing your ERP system. They’ll give you a quantifiable means of measuring performance, and they’ll provide an indicator of how well your new systems and processes are working.
When KPIs are not met, you should reassess your ERP project plan to determine if you’re following ERP best practices.
How to Convince Executives
There are several reasons executives may be hesitant to invest in ERP. Obviously, one of those is the cost. Another is risk aversion.
So, besides developing a business case, how can you gain the support of your leadership team?
1. Anticipate Questions
Executives are held responsible when an ERP implementation fails. As a result, they often err on the side of caution when it comes to expensive technology investments.
That said, when you approach the executive team, don’t just present the reasons why you should adopt the new technology. Think through the potential reasons why you shouldn’t, and come prepared with answers to objections such as:
- Our IT team doesn’t have the time to spend on implementation.
- Our legacy systems are too old to work with a new ERP system.
- Our processes are too complex for an out-of-the-box product.
- Our data won’t be secure.
2. Demonstrate Long-term Usability
In the long-term, outdated technologies can become hard to use and expensive to maintain. Modern ERP systems, on the other hand, are user-friendly and seamlessly integrate with technologies you might adopt in the future. This is important information to communicate to executives.
In fact, the more information you have about the ERP industry, the easier it will be to demonstrate long-term usability. That said, here’s some information that may pique executives’ interest:
- When most companies implemented their current ERP system, they probably didn’t have as many options as they do today. Cloud ERP systems and niche solutions are just two examples of areas that have become a greater focus for ERP vendors during the last decade.
- Along with this proliferation of options comes lower costs and more financial flexibility that translates to a better return on investment.
Additionally, you may want to talk about operational considerations unique to your business. For example:
- Most companies are struggling to find sources of growth and don’t need any additional headwinds to slow their progress. Even when demand for our product is strong, the last thing we need is an operational framework that can’t deliver to that demand. A new ERP system – along with more efficient business processes – would enable our company to scale and grow faster.
3. Build Credibility Through Case Studies and Reports
Corporate decision-makers need data to rationalize an investment. Most ERP vendors can provide extensive resources to help you build your business case, like a success story from another company in your industry.
4. Set a Realistic Timeframe
Implementing an ERP system doesn’t happen overnight. While executives may want immediate results, it’s better to give them realistic expectations. You should account for production testing, user training and data migration. Map out each milestone and consider building in extra days for unexpected roadblocks.
8 Reasons to Replace Your ERP System
Ultimately, building a business case is about providing compelling reasons to replace your current technology. Following are some reasons you may want to include in your business case:
1. Your Legacy System is Hindering Your Growth
The most obvious reason for an ERP implementation is simply to replace your legacy system. There comes a time in the trajectory of every company when the CIO or other executives recognize that their current software isn’t cutting it anymore.
There are several reasons a legacy system would become a burden. One is the proliferation of workarounds. If the business processes that your current system supports have changed, users may be relying on workarounds to perform their daily functions.
Workarounds are exactly what their name implies – extra steps performed in a system to work around missing functionality required to complete a task. Workarounds cause inefficiencies, and in turn, can increase costs and create unhappy employees.
Another reason companies replace their legacy systems is to increase employee satisfaction. A younger workforce may find it difficult to use the existing application and find newer software more attractive and even familiar. Newer technologies follow similar design patterns to consumer applications of which younger generations are already experts.
Keeping your workforce engaged has a direct impact on employee retention, which is important for staying competitive in any industry.
2. Your Company is Going Through Digital Transformation
One of the biggest shifts in the IT paradigm related to digital transformation is accepting that business applications can live in the cloud and don’t need to be on-premise to be serviced. When a company decides to transform its IT infrastructure from in-house to a cloud-based setup, most applications require a major upgrade or need to be retired and replaced.
Another shift related to digital transformation is companies acquiring new, modern applications to perform ancillary functions. For example, suppose a company implements a new expense tool. Both employees and management alike are loving the new tool as it allows an easy way to submit, view and approve expenses from any kind of device.
This scenario may not seem like it has anything to do with needing new ERP software, but what if the company has several of these examples and none of the applications integrate with the current ERP solution without heavy customization? A new system would most likely be more efficient and beneficial than creating all those custom interfaces.
3. You Need to Scale Your Business
When business is good, it grows, and with growth comes a need for a more robust enterprise backbone.
If your company has substantially expanded since you first implemented ERP, you may be outgrowing your system – depending on your ERP software scalability. There are some ERP systems that are built for small to medium sized businesses and others that are built for large enterprises. Still, others are flexible and scalable despite the size of the company.
Here are some telltale signs that your business could benefit from new ERP software to scale your business:
Performance is Slow in the Current System
Due to increased transactional volume, the performance of some ERP solutions may slow depending on their architecture. This will become apparent when users submit tickets for reports that take longer than normal to run or when batch jobs are not completing in the time they are allotted.
Intermittent Issues and Outages
If your ticketing system is constantly filled with users reporting outages and issues, your ERP system likely is not keeping up with the business demand. A key indicator is time-out related issues. Once you start seeing an influx of these, you’ll know it’s time to make a change.
If a new ERP solution is implemented for this reason, it’s a smart idea to pay particular attention to performance requirements and load testing throughout the implementation.
4. You Have Unreliable Data
One of the worst crimes a business application can commit is to provide bad data to users and customers. If your current system is providing inaccurate data to customers or faulty data is being used in demand forecasting, it’s time to implement a new system.
This also means you need to focus on ERP data migration. Without meticulous data management, your company will have to deal with inaccurate or duplicate data.
However, with strong data management and a modern ERP system, you will be able to seamlessly integrate the different aspects of recordkeeping and data processing. This enables your workforce to dedicate their efforts to actions that drive tangible results rather than on trying to keep company data up to date.
5. You Need Better Business Intelligence
One of our past clients is a mid-size international retail chain. They had an extremely successful business model, but they hadn’t cracked the code on how to integrate and make sense of all their customer data. Many companies are in the same boat, with plenty of data to sift through, but little in the way of ERP business intelligence.
If your company has difficulty understanding, predicting and making informed decisions, you may need a new system with advanced business intelligence.
6. You Want to Cut Costs
One of the first places a company looks to reduce costs is the IT department. After some analysis, a CIO or business leader could find that moving to a new ERP system would save the company a significant amount. Cost savings could come in the form of lower cost licensing and savings on custom support fees:
Lower Licensing Costs
Different vendors have varying licensing models – some can be considered a premium while others are in the affordable range.
Comparing your licensing cost for your current ERP solution to others in the market requires reaching out to the sales teams of different ERP vendors. It may seem too early when you’re simply trying to analyze the costs, but bringing in different vendors can actually save costs in the long run as the sales teams are fighting for your business.
If this seems a little intimidating, Panorama offers ERP selection and contract negotiation services where they serve as your advocate in meetings with vendors. Our experienced team can help you make the right decision for your company when selecting a new ERP solution.
No Custom Support Fees
If your company is currently paying vendor fees to support custom applications, this may be another place to save. Implementing new ERP software provides the opportunity to realign your business processes with industry standards, allowing you to drop custom support and utilize out-of-the-box capabilities of the system.
7. Upgrading Your Existing ERP
Another reason for an ERP project is the need for a software upgrade. There are a few key reasons for performing an upgrade, each with slightly different implications:
The Current Software Version is Sunsetting
Software vendors can’t support all versions of a product indefinitely, and with that constraint comes the need for customers to upgrade. Typically, when a vendor has a major version of their software approaching the end of its life in terms of technical support, they will proactively reach out to customers to help them through a transition plan.
If your company is facing a software end of life scenario, it’s important to weigh the pros and cons of upgrading versus moving to a different vendor that may better suit your unique needs.
Bug Fixes are Included in the New Release
Oftentimes users will be resourceful and find workarounds to system shortcomings to complete vital tasks. If an upgraded version has fixes to these workarounds, the justification for upgrading is satisfied immediately.
8. The Rate of Technological Change is Accelerating
This is true across all industries. For example, one of our past clients was a business-to-business distributor of lawn care products, and their business was being disrupted by technology innovators and industry behemoths.
While this industry niche may sound old-school and unaffected by leading-edge technology, they were being as severely disrupted as many retailers. Their customers were demanding quicker and more transparent service, and their suppliers expected a more streamlined experience.
Even if you think your industry is remaining pretty much the same, technology is raising the bar for how your internal and customer-facing processes should look. For example, another of our past clients was a steel manufacturing company that needed help defining and implementing an IT digital strategy so they could more efficiently meet customer expectations.
This industry is about as far from technological innovation as you can get, so if their business is being impacted by technological change, then chances are that yours is, as well.
Why Businesses Should Replace Their ERP Software at Least Every Ten Years
As the below graphic depicts, companies diverge from their ERP software over time:
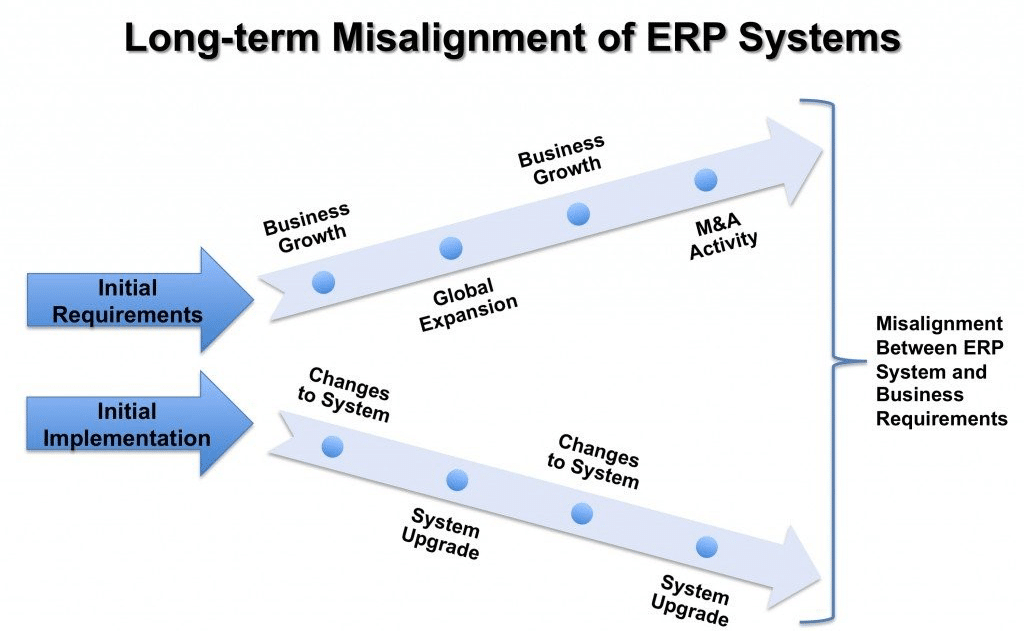
Technology – if implemented correctly – is relatively well-aligned with the business after an ERP implementation. However, this alignment diverges an increasing amount over time. We find with many of our clients that it is on average a 10-year period before this misalignment reaches a boiling point.
Following are two reasons for this misalignment:
1. Changes to the Business
The biggest of the two drivers of this divergence are changes to the business. Ten years is an eternity in a fast-changing global economy, so what a business needs today is very likely to be different from what it needs in the future.
Companies grow, acquire other companies, expand overseas, diversify their product lines and initiate other changes to their business that cause their business requirements to evolve. Unfortunately, not all ERP software can keep up with these changes.
2. ERP Software Changes
To complicate things, the software itself is also a moving target. ERP vendors generally release minor upgrades to their software multiple times a year, with major upgrades every few years. With these new releases come changes that may not be aligned with the business’ needs.
Granted, the whole point of these upgrades is to improve and enhance the functionality of the software, so in a perfect world these changes would keep up with changes to your business. However, this isn’t always the case.
Gaining Executive Buy-in Takes Time
If you use this blog post to help craft an ERP business case, you’re likely be met with open-mindedness. However, this takes time and persistence. Be patient and keep quantifying those benefits!
Panorama’s ERP consultants can support you in your quest to convince executives. Request a free consultation below to learn about some of the quantifiable benefits that can be used in a business case.